
production
The GinkGo bike is a new cargo bike concept that is designed and manufactured in Sweden.

It all starts with aluminum tubing. Thanks to its balance between strength and ductility, we use 6061 aluminum alloy.
​
The tubes are machined to ensure a perfect fit. In the next production step, the tubing is bent to precisely the right angles.
Aluminum alloy tubing is the main ingredient of the GinkGo frame.
The bent tubing is then assembled into our precision welding jig, together with bottom bracket shell, head tubes, stays and drop outs. Obtaining high quality welds is critical for lasting durability, and we use one of Sweden's best aluminum welders for this.
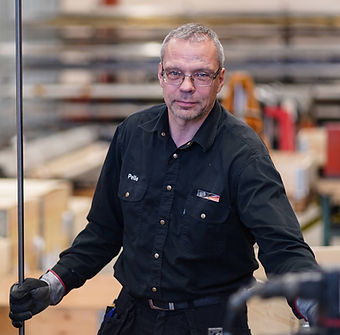
Per-Erik “Pelle” Hjälmkvist at BS Rörbockning.
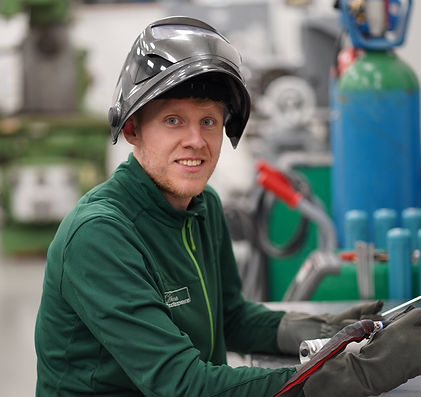

Tomas Norlander next to the oven at the GinkGo factory in Stockamöllan.
Niklas Hartler at Divina Performance.
After mechanical alignment the frame is heated up once more–this time to 175 °C for 8 hours–to finalize the heat treatment and acquire the so-called T6 state for the metal. Once all mounting surfaces have been covered, the frame is sandblasted to produce an optimal surface finish for powder coating.
​
​We powder coat the frame in one of our popular stock colors, or another RAL color upon request. After the paint job, bottom brackets and head tubes are reamed to ensure a perfect fit, and all threads are cleaned with taps.
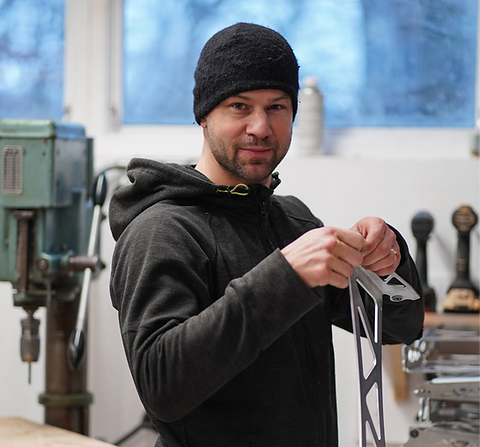
Martin Norlander assembling a GinkGo kickstand.

Stickers are applied and our custom lightweight steering rod and kickstand are fitted to the frame. The frame is then ready to be packaged and shipped as a bare frame set; with panels, child seat or other accessories; or as a complete bike.
​
We put a lot of work into each GinkGo and expect them to be used extensively over the years to come.
Tomas Norlander uses unconventional product testing methods.